Paddy cultivation, an arduous process with farmers often dissatisfied with the yield, is one of the main sources of livelihood in India’s north-east state of Assam. Things could soon change, however, with ‘serial innovator’ Uddhab Bharali designing an energy-efficient, low-cost machine that is expected to double the rice yield while making the entire process easier and less time consuming.
Based in Lakhimpur on the northern bank of the Brahmaputra, Bharali, who has about 100 innovations under his belt, says his vision is “to change the agriculture scenario”. From simple tasks like pomegranate deseeding and peeling cassava to bigger ones like cement brick making and processing tea, Bharali has designed machines for a range of uses. And, like his other designs, the paddy seeding technique is environmentally responsible and aimed at boosting the economy of the state.
“Conventional rice cultivation yields 10 muna or 40 kg of rice from one bigha (about one acre) of land. With my paddy seeding machine the yield will be double,” Bharali said.
Resembling a cart, the machine, priced at a modest Rs.3,000 (about US$45), will also yield better quality rice because the seeds are encased in plant protection and germinating material. Supported by the Assam Agricultural University, the ‘Uddhab’ machine is now ready to be introduced to the farmers’ community.
Explaining how the machine works Bharali said, “In the traditional form of paddy cultivation, the practice of preparing the seed bed, its maintenance for a month and then transplanting the ‘kothiya’ (paddy shoot) to the puddle soil bed is cumbersome and labour intensive. My manually operated machine will plant the encased paddy seeds into the soil at an exact 10 inch gap, thereby removing the transplantation process.”
“The reason why transplantation is done is to maintain this gap between two plants for an optimum production. The seeds are thrown at random in the beginning but they would not grow into healthy plants if allowed to grow in such close quarters.”
The machine will also dig the soil and make a trench 1.5 inches deep as it moves along and drops the seeds at the given interval. At this depth, the seeds need minimum amount of irrigation and give best results, the innovator, who is in his 50s, said.
Body of work
Most of Bharali’s innovations are agro-based. His aim, he says, is to help farmers and others make their life simpler and more sustainable.
“When common sense is applied in a common place, technology is born. It is not necessarily found in fancy labs,” he said.
He is also working on a contraption to retrieve rice grains from plants. “Why does harvesting have to be so tough? Why do you need to cut the whole plant to get the grains? I am designing a manual cutter with which one can just retrieve the grains and not have to battle the whole plant.”
Among his popular innovations is the mini tea plant for green tea and Crush Tear Curl (CTC) tea, aimed at helping the growing population of small tea growers of Assam. “The plant consumes only 2 kilowatts of electricity, equivalent to the power consumption of an average household, and can be run by semi-skilled labour. Green tea from this machine has fetched Rs.3,000 per kg in tea auctions. And the machine only costs Rs. 3.75 lakh (about US$5,000). There is already a huge demand for it,” Bharali said.
The machine, he hopes, will “end exploitation of small tea growers by big tea companies”.
“Already 21 tea plants have been sold, and the demand is much higher. Not only does it make a small tea grower independent and helps boost its profits, it also employs people. One tea plant requires 15 people to work,” he added.
His cement brick-making machine is another marvel that can be operated by anyone—including people with disabilities. “A person who has lost a hand faces immense difficulties in earning a livelihood. The brick-making machine is manually operated one and can be used by such a person too. It opens up a whole gamut of opportunities,” Bharali said.
Priced at Rs.40,000 (US$600), more than 200 pieces of this machine have been sold so far.
Environmental benefits
Apart from the economic benefits —and his machines are exported too—Bharali says that each one is environmentally responsible. “The brick kilns for example are a major source of pollution, but the one that I have designed causes no such harm to the environment. My innovations are mostly manually operated—which keeps the cost in check too—and consumes minimum power,” said Bharali, who received several awards, including the President’s award for grassroots innovators in 2010.
Ironically, Bharali is a ‘drop out’. Despite being a good student, he had to leave his studies in while in college because of abject poverty.
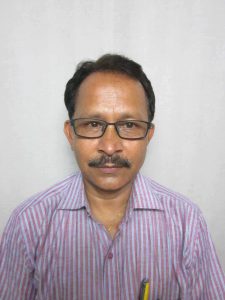
“People who craft success stories usually say that they started their journey from zero; I started from minus Rs.18 lakh (US$27,000). That was the amount of debt on my family,” he said. He lost his father early, and then his elder brother. But Bharali refused to give up.
His early days of creating machines to simplify laborious tasks like peeling garlic or cassava were challenging, he says, recalling how he was constantly mocked for not doing something “worthwhile”.
But he was undeterred. From 1990 to 2006, he had created 24 machines. Finally, his cassava peeling machine earned him international repute but because of lack of finances to manufacture the machine from the prototype, the technology was transferred to a company through the National Foundation of India.
“By then I realised that I could not let go of my hard earned opportunities and decided to try my hand in making the pomegranate deseeding machine that experts were still struggling to make. Eventually I succeeded and it was featured on the Discovery Channel,” he said.
As fame reached out to him, Bharali realised that the prototype could be improvised.
“After struggling for six months with it, I came home one dark and rainy night with a bag of pomegranates on my motorcycle. I kept thinking about the machine, and about 100 metres from my house, I stopped and out of frustration, chopped and kicked the fruit. The pomegranate rolled away, hit a big stone, bounced and the seeds came out neatly. I went back home and my improvised pomegranate deseeding machine was ready in 72 hours,” he said with pride. Orders started pouring in, including for export to Turkey and the US after that, and he finally made his mark as an innovator.
He was also awarded a doctorate from the Assam Agricultural University. He is now a guest faculty member in all the prominent varsities of Assam and is invited to the various Indian Institutes of Technology (IITs) for lectures.
Bharali’s success and fame has however failed to raise his hunger for money. Most of his innovations are available commercially and are exported as well, and he holds copyright for each of them, but a large part of the profit goes into his research and in supporting 21 families whose main breadwinner is disabled. His favourite innovation, in fact, is the one that helps people with disabilities—those who have lost their hands—to eat and clean themselves.
Bharali is also in the process of setting up an orphanage and an old age home and is setting up a museum at his humble abode for students to take a look at all his innovations and “get inspired”.